
2730 COMBINATION RIPPER
Combination Ripper
- Adjust depth in six seconds on the go
- In-cab control of each functional area
- 1/10th-in. (2.5-mm) accuracy
- Expanded tractor compatibility
View Product Brochure
Features
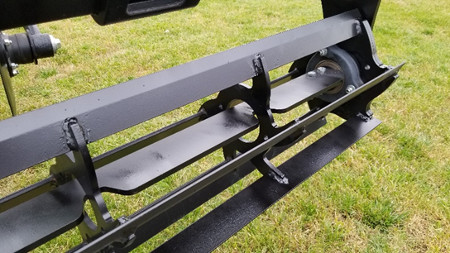
The internal basket scraper allows for a uniform field finish in wet conditions because the baskets will not need to be raised out of ground to avoid plugging and can stay in the ground 100 percent of the time.
This is available as an option for the knife-edge basket.
The 2730 Combination Ripper is available in five machine configurations:
- 7S24 – 7-standard rigid frame with 610-mm (24-in.) spacing
- 9S24 – 9-standard rigid frame with 610-mm (24-in.) spacing
- 9S24 – 9-standard folding frame with 610-mm (24-in.) spacing
- 11S24 – 11-standard folding frame with 610-mm (24-in.) spacing
- 13S24 – 13-standard folding frame with 610-mm (24-in.) spacing
Model | Working width | Transport width | Transport height |
7S24 Rigid – Individual blades | 4.27 m (14 ft) | 6.07 m (19 ft, 11 in.) | 2.49 m (8 ft, 2 in.) |
7S24 Rigid – Disk gangs | 4.27 m (14 ft) | 5.74 m (18 ft, 10 in.) | 2.49 m (8 ft, 2 in.) |
9S24 Rigid – Individual blades | 5.49 m (18 ft) | 6.86 m (22 ft, 6 in.) | 2.49 m (8 ft, 2 in.) |
9S24 Rigid – Disk gangs | 5.49 m (18 ft) | 6.86 m (22 ft, 6 in.) | 2.49 m (8 ft, 2 in.) |
9S24 Folding – Individual blades | 5.49 m (18 ft) | 5.82 m (19 ft, 1 in.) | 3.30 m (10 ft, 10 in.) |
9S24 Folding – Disk gangs | 5.49 m (18 ft) | 5.82 m (19 ft, 1 in.) | 3.35 m (11 ft, 0 in.) |
11S24 Folding – Individual blades | 6.71 m (22 ft) | 5.59 m (18 ft, 4 in.) | 3.81 m (12 ft, 6 in.) |
11S24 Folding – Disk gangs | 6.71 m (22 ft) | 5.69 m (18 ft, 8 in.) | 3.81 m (12 ft, 6 in.) |
13S24 Folding – Individual blades | 7.92 m (26 ft) | 5.59 m (18 ft, 4 in.) | 4.39 m (14 ft, 5 in.) |
13S24 Folding – Disk gangs | 7.92 m (26 ft) | 5.69 m (18 ft, 8 in.) | 4.19 m (13 ft, 9 in.) |
The 7.90-m (26-ft) 2730 delivers a 44 percent increase in productivity over the largest 5.50-m (18-ft) John Deere 2700 Mulch Ripper. The 2730 fits into a tillage system that includes the following secondary tillage tools:
- 2230 Field Cultivator
- 2330 Mulch Finisher
- 2630 Series Disks
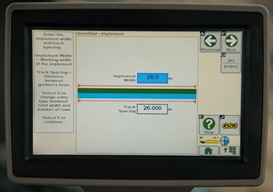
The ability to set the true width of the 2730 into the track spacing setting on the GreenStar display delivers a 6 percent increase in productivity allowing the operator to cover more acres in the same amount of time versus the competition. The true width is achieved through additional disk blades along with their tapered design to ensure consistent coverage and a level finish across the entire tillage pass.
The 2730 is a combination ripper that integrates four operational areas into one system. These four areas consist of disk blades, ripper shanks, rear closing disks, and finishing attachments. The ability to quickly and conveniently customize these components independently offers reduced cost of operation and maximum productivity.
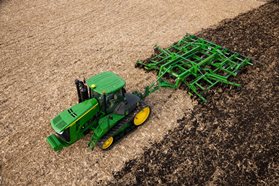
The disk blades eliminate the need for multiple residue sizing passes into one single pass that reduces surface residue levels by 60-80 percent. The 2730’s ability to mix and bury more residue leads to faster soil warming in the spring all while reducing negative impacts of disease and insect pressure.
The ripper shanks accomplish full hardpan fracture across the entire soil profile with their 610-mm (24-in.) spacing in order to create a porous air and water environment for root development. Along with the ripper shank’s side-to-side spacing, it also features a 1270-mm (50-in.) fore-aft spacing that improves residue disbursement and contributes to the machines nearly plug-proof performance.
With TruSet™ or manual adjustment, the operator can set this system to leave a uniformly mounded profile covering each ripper track, or it can be adjusted to obtain a smooth, level surface ideal for minimum preparation for the next spring’s seedbed. With the walking tandem action, the closing system can follow the contour of the ground and eliminate plugs leading to a more consistent finish.
To achieve optimal field levelness and clod sizing, the operator can control the finishing attachment with in-cab, hydraulic controls. The finishing attachments can be set to constant down pressure, float, or in wet field conditions, rise completely out of the ground. This will insure the seedbed is best prepared for the least amount of pre-plant seedbed tillage passes before planting.
Typical percentage of residue cover remaining from the 2730 Combination Ripper is listed in the table below. These percentages do not take into account variables such as the conditions of the residue, speed, and soil type.
NOTE: Percentages assume disk blades are operating at 152 mm (6 in.) of depth.
Starting residue cover (percent) | Remaining non-fragile* residue cover (percent) | Remaining fragile** residue cover (percent) | ||
57-mm (2.25-in.) point | 178-mm (7-in.) point | 57-mm (2.25-in.) point | 178-mm (7-in.) point | |
100 | 30 | 27 | 15 | 12 |
90 | 27 | 25 | 14 | 11 |
80 | 24 | 22 | 12 | 10 |
70 | 21 | 19 | 11 | 8 |
60 | 18 | 16 | 9 | 7 |
50 | 15 | 14 | 8 | 6 |
40 | 12 | 11 | 6 | 5 |
*Non-fragile residue includes crops like corn, sorghum, and wheat (more than 1586 L [45 bu]).
**Fragile residue includes crops: soybeans, edible beans, peas, wheat (less than 1586 L [45 bu]), sunflower, peanuts, and cotton.
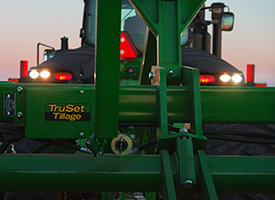
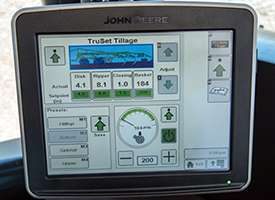
In just six seconds, 2730 Combination Ripper operators can manage their changing field conditions by making on-the-go adjustments for the entire implement from the tractor cab. TruSet enables users to adjust depths for the disks, rippers, and closing disks, and adjust the pressure on the active hydraulic rolling baskets – all while covering acres.
As conditions change throughout the field, operators running the 2730 with TruSet can quickly and efficiently respond to varying soils, compacted areas, heavier residue, and moisture. Making customized adjustments that respond to these agronomic factors help customers maximize their yield potential.
Adjusting the 2730 Combination Ripper with TruSet can be done up to 200 times faster than the manual adjustment process using single-point depth control and cylinder stops. With short windows to perform tillage work, that critical time savings could be the difference in getting fields worked or not.
Operators no longer have to sacrifice machine performance by deciding to forgo manual adjustments throughout the field. At the touch of a button, TruSet users can quickly respond to changing conditions such as running deeper over end rows or shallower on hilltops and lighter soils. TruSet users can optimize their 2730 depth adjustments to maximize tractor performance for more efficient fuel use, and lower overall operating costs.
TruSet also add precision to tillage operations. The system offers depth accuracy of 2.5 mm (0.1 in.) and more than doubles the number of depth setting increments on the 2730 Combination Ripper. This finite level of control enables 2730 operators to create the ideal soil structure, and evenly size and distribute residue for maximum yield potential.
Functional area | 2730 adjustment settings without TruSet | 2730 adjustment settings with TruSet | Improvement |
Front disks | 32 | 80 | 150 percent |
Rippers | 47 | 95 | 100 percent |
Closing disks | 20 | 50 | 150 percent |
Single-point depth control is standard on all 2730 Combination Rippers. Single-point depth control provides the option for users to manually set implement depth, even with TruSet.
Functionality
This advanced tillage technology, available exclusively from John Deere, provides operators with real-time knowledge of the settings for each functional area on the implement. With a working tillage width of up to 7.9 m (26 ft) on the 2730, consistent tillage performance can be easily obtained from front to back across all four functional areas of this machine.
Both the set points entered by the user and the actual running depth or pressure for each area on the implement can be easily referenced for assurance of desired tillage outcomes. Once actual set point is validated and configured to the display in the cab, operators are able to make independent adjustments to the disks, rippers, or closing disks with accuracy within one tenth of an inch. Four memory set points enable operators to save different combinations of settings for their most common field conditions.
The independent adjustability of each area on the 2730 helps ensure TruSet users are efficiently managing residue and creating the ideal soil structure. By responding to conditions as they change throughout the field, TruSet operators generate better-quality tillage performance with the first pass.
Compatibility
TruSet is compatible with John Deere and competitive tractors. The following chart identifies the components needed to operate TruSet on a 2730 Combination Ripper with a GreenStar™ system-ready tractor.
| John Deere 30 Series | John Deere 20 Series | Competitive tractors |
Yes | Yes | Yes | |
No | Yes | Yes |
Like the TruSet Tillage System, the compatibility kit will be available as a field-installed option that can be ordered with the 2730 or through aftermarket parts. The compatibility kit includes an implement add-on valve and installation components.
All model years of the 2730 can be retrofitted with TruSet.
Additional information
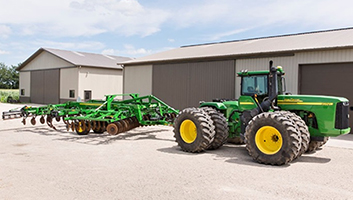
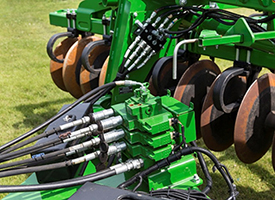
Adding the TruSet compatibily kit to the TruSet Tillage system enables operators of competitive tractors and older John Deere tractors to adjust their depth and pressure settings on the go from the cab.
With the TruSet compatibility kit, TruSet can be run on the following GreenStar™ system-ready tractors:
- John Deere 20 Series Tractors and older
- Competitive tractors
Like the TruSet Tillage system, the compatibility kit will be available as a field-installed option that can be ordered with the 2730 Combination Ripper or through aftermarket parts. The compatibility kit includes an implement add-on valve and installation components.
All model years of 2730 can be retrofitted with TruSet. The following chart identifies the components needed to equip TruSet on a 2730 with a GreenStar ready tractor.
TruSet product | John Deere 30 Series Tractors and newer | John Deere 20 Series Tractors and older | Competitive tractors |
TruSet Tillage System | Yes | Yes | Yes |
TruSet compatibility kit | No | Yes | Yes |
Option code | Attachment | Description |
9407 | BKK10342 | TruSet compatibility kit for 2730 Combination Ripper |
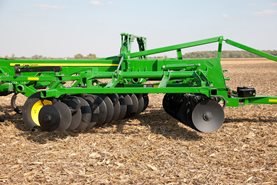
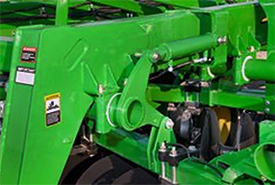
The 2730's large 660-mm (26-in.) disk blades are hydraulically adjustable and are set in a tandem-type configuration. The disks are available in either individual disk blades or gang-type configuration. The front and rear blades are set at an 18-degree angle on either 460-mm (18-in.) spacing for individual or 280-mm (11-in.) spacing for gang to provide an aggressive disking action.
The disks can be adjusted in-cab to be raised completely out of the ground or lowered to a maximum in-ground depth of 203 mm (8 in.). The disk blades operate in constant down-pressure and the optimal operating depth can be set from the cab with TruSet™ or manually using stop collars on the hydraulic cylinder. The ability to independently adjust the front disks based on varying conditions allows the operator to optimize desired residue sizing and mixing.
The larger disks are designed of high-quality steel and made from a manufacturing process for extended performance provide the following benefits:
- Size and bury residue
- Level the soil profile
- Mix the surface residue
- Give full-width tillage up to 200 mm (8 in.) deep
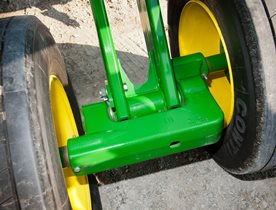
Walk-Over tandem wheels with larger tire options offer maximum support, stability, and flotation in the field. The staggered wheel design provides additional room for residue flow and obstacles all while providing a consistent working depth in uneven ground.
The Walk-Over tandem mainframe wheels come equipped with 57-mm (2.25-in.) plug-in spindles and eight-bolt hubs on the 7- and 9-standard models, and 79-mm (3.125-in.) plug-in spindles and ten-bolt hubs on the 11- and 13-standard models. The 11- and 13-standard models feature an active-hydraulic wing wheel to ensure a consistent operating depth with uniform leveling. These active-hydraulic wing wheels allow the 2730 machine to better follow the contour of the land versus rigid-mounted wing wheels on competitive models.
Available tires options are listed below:
Model | Mainframe tire | Wing frame tire |
7-Standard 4.30 m | 12.5L-15 FI F LR* | --- |
9-Standard 5.50 m | 340/65R18 Goodyear* | --- |
9-Standard 5.50 m | 340/65R18 Goodyear* | --- |
11-Standard 6.70 m | 550/45R22.5 Alliance* | 12.5L-15 FI F LR Goodyear* |
13-Standard 7.90 m | 550/45R22.5 Alliance* | 12.5L-15 FI F LR Goodyear* |
*Base tire option
With the option to upgrade to the market’s largest 10-bolt hub, heavy-duty 445/50R22.5 or high-flotation 550/45R22.5 tires on all models, the weight of the machine is evenly transferred to the ground to ensure stable transport and operation. All mainframe tires available produce maximum flotation and durability for in-field performance with 33 percent more tire-to-ground engagement than the competition.
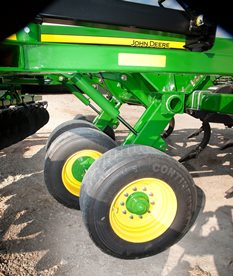
Goodyear is a trademark of The Goodyear Tire & Rubber Company.
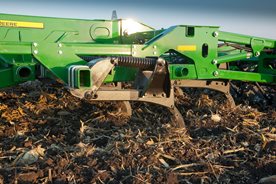

The 2730 delivers improved residue flow by increasing the overall frame length and underframe clearance along with the fore-aft spacing of the ripper shanks.
The 1270-mm (50-in.) fore-aft spacing maximizes residue disbursement and 953 mm (37.5 in.) of underframe clearance contribute to the machines nearly plug-proof performance. The 2730 features 610-mm (24-in.) side-to-side spacing that accomplishes full hardpan fracture across the entire soil profile to create a porous air and water environment for root development and plant nutrient uptake.
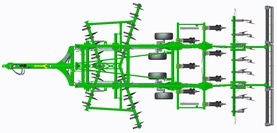

For added durability and increased soil penetration, the 2730 boasts the largest and heaviest frame in the industry. The overall weight of each model ensures consistent machine performance. In high residue areas, 953 mm (37.5 in.) of underframe clearance results in reduced plugging and increased residue flow to maintain productivity and uptime.
Model | Weight* |
7S24 Rigid – Individual blades | 7167 kg (15,800 lb) |
7S24 Rigid – Disk gangs | 7756 kg (17,100 lb) |
9S24 Rigid – Individual blades | 9072 kg (20,000 lb) |
9S24 Rigid – Disk gangs | 10,070 kg (22,000 lb) |
9S24 Folding – Individual blades | 9435 kg (20,800 lb) |
9S24 Folding – Disk gangs | 10,433 kg (23,000 lb) |
11S24 Folding – Individual blades | 13,608 kg (30,000 lb) |
11S24 Folding – Disk gangs | 14,696 kg (32,400 lb) |
13S24 Folding – Individual blades | 14,288 kg (31,500 lb) |
13S24 Folding – Disk gangs | 15,558 kg (34,300 lb) |
*Weights listed are for models equipped with no leveling attachment
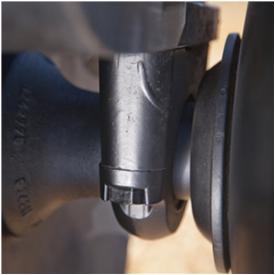
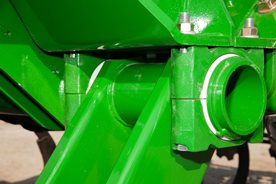
Sealed, maintenance-free bearings on the 2730 Combination Ripper results in reduced downtime for the operator.
The greaseless bearings increase productivity by reducing the amount of time needed to service the 2730 before operation and allowing operators to spend more of their valuable time in the field. Independent testing results show the 2730 bearings have 30 percent less contamination than the competition. The maintenance-free bearings have been extensively field tested to stand up in tough conditions providing longer bearing life.
The 2730 employs a high-density polymer liner that allows the bearings to dynamically align the shaft in rough field conditions. The cast-bearing housing also allows for additional protection with the bearing wear guard built-in which leads to increased reliability.
The 2730 features 78 percent fewer grease points than major competitors resulting in less, time-extensive maintenance and improving field productivity by up to 3 ha (7.5 acres) per day.
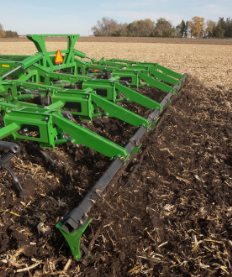
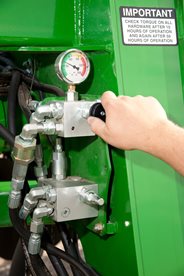
The 2730 comes equipped with the optional hydraulically adjustable finishing attachments to achieve the desired field finish. The hydraulic rolling baskets can be set to three hydraulically controlled positions from the comfort of the cab. The heavy-duty coil tine harrow is rigid mounted to the frame and depth adjustments are made according to the rear closing disk system. Based on field finish needs, the 2730 less harrow option is also available.
The finishing attachments come in a round-bar, knife-edge, or coil tine configuration and prepares field for a reduced amount of secondary tillage passes before planting. Below are the benefits of each attachment:
- Knife edge – better option in heavier, wet soils. Recommended basket for rocky soil types.
- Round-bar – best in dry conditions for clod sizing and firming. Slightly more prone to plugging over the knife edge.
- Heavy-duty coil tine harrow – preferred finishing attachment in heavy, poorly drained soils.
The rolling baskets can be hydraulically set to three different operating positions based on field conditions:
- Down pressure – a gauge on the front of the 2730 allows operators to set basket down pressure to ensure constant ground contact. Down pressure also allows for better sizing of slabs, clods, and root balls and will leave a level soil profile.
- Float – the baskets can be put in the float position using the selective control valve (SCV) on the tractor. This allows the weight of the basket to roll over the ground.
- Raised – the baskets can be lifted off the ground when encountering a wet area of the field to help eliminate any chance of plugging.
The active hydraulic down-pressure system allows the operator to increase the down pressure on finishing attachments up to 8274 kPa (1200 psi). Adjustments are made with a dial located next to the gauge. Down pressure should be set using the gauge and operated from the cab.
The GoTill mobile application from John Deere is available on Apple® and Android™ smartphones. This application is a user-friendly system for operators to work their way through the initial recommended 2730 machine setup in order to optimize machine performance.
GoTill features a maintenance section and a notes section with photo functionality to give operators a premium experience when setting their machines. GoTill is also a great guide to use for settings and adjustments as field conditions differ to document changes made throughout the tillage season.
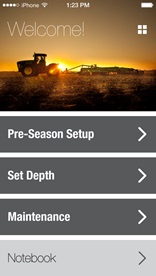
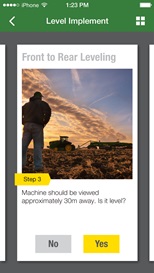
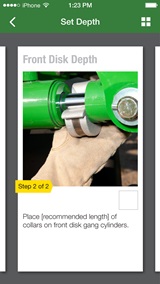
GoTill mobile screenshots |
GoTill is an impactful resource that can be used in addition to the operator’s manual settings guide that comes standard with all John Deere tillage equipment. GoTill is available on Apple App Store® and through Google Play™.
Android and Google Play are trademarks of Google LLC. Apple and Apple App Store are trademarks of Apple Inc.
Specifications
Compare the specifications of up to 4 models
Key Specs | 2730-combination-ripper Current Model |
---|---|
Working width | Option 1: 4.3 m 14 ft Option 2: 5.5 m 18 ft Option 3: 5.5 m Option 4: 6.7 m 22 ft Option 5: 7.9 m 26 ft |
Transport width | Option 1: Individual blades: 6.1 m 19.9 ft Disk gangs: 5.7 m 18.8 ft Option 2: Individual blades: 6.9 m 22.5 ft Disk gangs: 6.9 m 22.5 ft Option 3: Individual blades: 5.7 m 18.8 ft Disk gangs: 5.8 m 19.1 ft Option 4: Individual blades: 5.6 m 18.3 ft Disk gangs: 5.7 m 18.7 ft Option 5: Individual blades: 5.6 m 18.3 ft Disk gangs: 5.6 m 18.3 ft |
Maximum operating depth | 40.6 cm 16 in. |
Operating speed | 8-11.3 km/h 5-7 mph |
Horsepower required per standard | 25.1-41 kW 34-55 hp |
Standards | Spacing 61 cm 24 in. |
Tool | |
Configuration | Disk - Disk - Ripper - Closing Disk - Finishing Attachment |
Option 1 | Rigid 7-standard on spacing of 61 cm 24 in. |
Option 2 | Rigid 9-standard on spacing of 61 cm 24 in. |
Option 3 | Folding 9-standard on spacing of 61 cm 24 in. |
Option 4 | Folding 11-standard on spacing of 61 cm 24 in. |
Option 5 | Folding 13-standard on spacing of 61 cm 24 in. |
Option 6 | |
Option 7 | |
Option 8 | |
Option 9 | |
Option 10 | |
Option 11 | |
Option 12 | |
Option 13 | |
Option 14 | |
Option 15 | |
Option 16 | |
Option 17 | |
Working width | |
Option 1 | 4.3 m 14 ft |
Option 2 | 5.5 m 18 ft |
Option 3 | 5.5 m 18 ft |
Option 4 | 6.7 m 22 ft |
Option 5 | 7.9 m 26 ft |
Option 6 | |
Option 7 | |
Option 8 | |
Option 9 | |
Option 10 | |
Option 11 | |
Option 12 | |
Option 13 | |
Option 14 | |
Option 15 | |
Option 16 | |
Option 17 | |
Transport width | |
Option 1 | Individual blades: 6.1 m 19.9 ft Disk gangs: 5.7 m 18.8 ft |
Option 2 | Individual blades: 6.9 m 22.5 ft Disk gangs: 6.9 m |
Option 3 | Individual blades: 5.7 m 18.8 ft Disk gangs: 5.8 m 19.1 ft |
Option 4 | Individual blades: 5.6 m 18.3 ft Disk gangs: 5.7 m 18.7 ft |
Option 5 | Individual blades: 5.6 m 18.3 ft Disk gangs: 5.6 m |
Option 6 | |
Option 7 | |
Option 8 | |
Option 9 | |
Option 10 | |
Option 11 | |
Option 12 | |
Option 13 | |
Option 14 | |
Option 15 | |
Option 16 | |
Option 17 | |
Depth | |
Transport clearance | |
Underframe clearance | |
Speed | |
Horsepower | |
Depth control | |
Option 1 | Single-point crank |
Option 2 | TruSet™ tillage |
Hydraulics | |
Option 1 | 4 SCVs (depth control, front disk, rear conditioner, optional rolling baskets) at 17,237 kPa 2,500 psi for optimum raise times |
Option 2 | 5 SCVs (depth control, front disk, rear conditioner, wingfold, optional rolling baskets) at 17,237 kPa 2,500 psi for optimum raise times |
Hitch | |
Design | Single tube |
Fore-aft adjustment | Hitch turnbuckle |
Standards | |
Spacing | 61 cm 24 in. |
Frame cross section | |
Standards, Option 1 | |
Trip force | Cushion-trip standard: 1,859.7 kg 4,100 lb |
Trip height | Shear bolt protected above: 33 cm 13 in. |
Type | Parabolic with or without wear shins, straight with wear shins |
Standards, Option 2 | |
Trip force | |
Trip height | |
Type | |
Standards, Option 3 | |
Trip force | |
Trip height | |
Type | |
Ground engaging components | |
Type | Wingless, LaserRip™ II points: 12.7 cm 5 in. 17.8 cm 7 in. 25.4 cm 10 in. |
Coverboards | On parabolic standards: 10.2 cm 4 in. 15.2 cm 6 in. 20.3 cm 8 in. |
Wear shin | |
Mulching disk components | |
Description | X-type configuration at front of tool |
Depth control | TruSet in-cab controls Single-point depth control |
Maximum depth | 20.3 cm 8 in. |
Type of standard | C-spring |
Base equipment blades | Solid spherical low-concavity disk blades: 660x6 mm 26x0.25 in. |
Blade spacing | Individual: 45.7 cm 18 in. Effective - 22.9 cm 9 in. Disk gang: 27.9 cm 11 in. Effective: 14 cm 5.5 in. |
Front frame angle | Fixed: 18 degree (angle) |
Rear frame angle | Fixed: 18 degree (angle) |
Spools | |
Bearings | Sealed, maintenance-free |
Scraper | Heavy-duty floating combination scraper (base option) |
Rear conditioner | |
Description | Solid-spherical low concavity closing disks (notched optional) |
Adjustments | TruSet in-cab controls Mechanical |
Base equipment blades | Individual dual mount: 45.7 cm 18 in. |
Bearings | Sealed, maintenance-free |
Type of standard | |
Wheels | |
Rear hitch | |
Approximate weight | |
Option 1 | |
Option 2 | |
Option 3 | |
Option 4 | |
Option 5 | |
Option 6 | |
Option 7 | |
Option 8 | |
Option 9 | |
Option 10 | |
Option 11 | |
Option 12 | |
Option 13 | |
Option 14 | |
Option 15 | |
Option 16 | |
Option 17 | |
Additional Features | |
Option 1 | Hydraulically adjustable finishing attachments Knife-edge rolling basket Round-bar rolling basket Coil-tine harrow |
Option 2 | |
Option 3 | |
Option 4 | |
Option 5 | |
Tires | |