
W200M WINDROWER
Windrower
- 200hp
- Integrated AutoTrac™ steering system helps maintain crop quality even at faster cutting speeds
- JDLink™ enabled
- Optional 24 mph transport speed
View Product Brochure
Features
M-spec cab
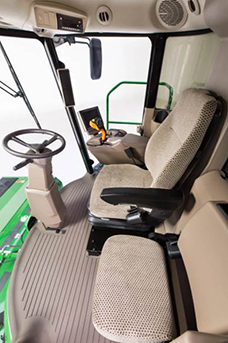
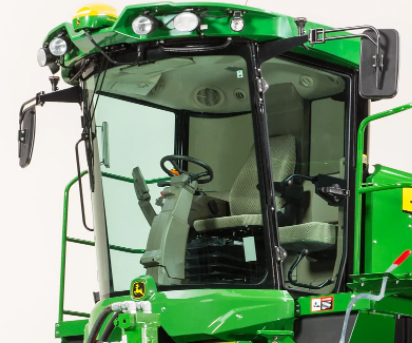
The W200M and W235M Self-Propelled Windrowers come with a cab that offers a comfortable and quiet working environment with plenty of visibility, storage, and features.
- JDLink™ system enabled
- AutoTrac™ assisted steering system ready
- Rear window tint
- Automatic temperature control
- Two halogen rear worklights
- Great visibility
- Operator’s seat with mechanical suspension
- Folding instructor seat
- AM/FM radio with Bluetooth® wireless functionality
- Tilt steering column
- Cornerpost display
- Two 12-V power outlets
- Sun visor
- Halogen lights
- Ergonomic multi-function lever
- 4200 CommandCenter™ Display
R-spec cab
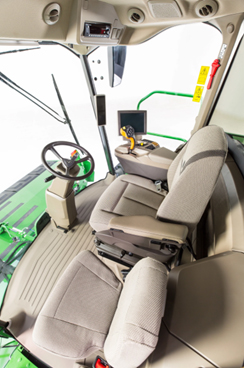
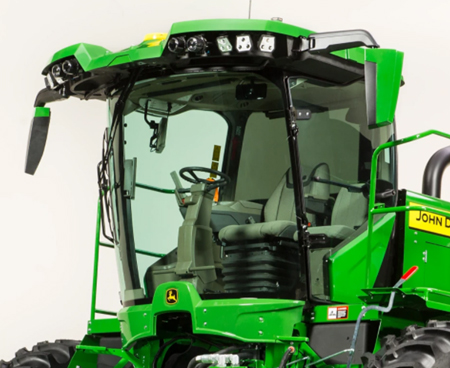
The R-spec cab comes in three different trim levels:
- Select
- Premium with air suspension seat
- Premium with active seat
|
Select |
Premium with air suspension |
Premium with active suspension |
|
Comfort and Convenience |
Seat |
|
|
|
Infotainment |
|
|
|
|
Interior upholstery |
Upholstery without right-hand storage |
Upholstery with right-hand storage |
Upholstery with right-hand storage |
|
Exterior styling |
Without exterior styling panels |
With exterior styling panels |
With exterior styling panels |
|
Visibility |
Lighting |
Halogen |
LED |
LED |
Mirrors |
Manual |
Electric heated |
Electric heated |
|
Sunshades |
Front |
Front/rear |
Front/rear |
|
Wipers |
Front |
Front |
Front |
|
Seat suspension |
Air (passive) |
Yes |
Yes |
No |
Active suspension |
No |
No |
Yes |
|
Precision Ag Technology |
Integrated StarFire™ receiver |
Integrated StarFire ready |
With Integrated StarFire |
With Integrated StarFire |
Extended display |
No |
No |
No |
Bluetooth is a trademark of Bluetooth SIG, Inc.
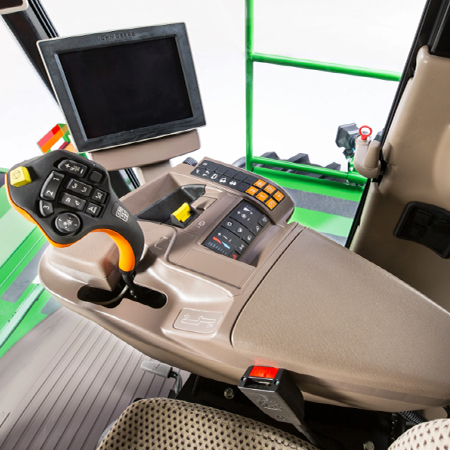
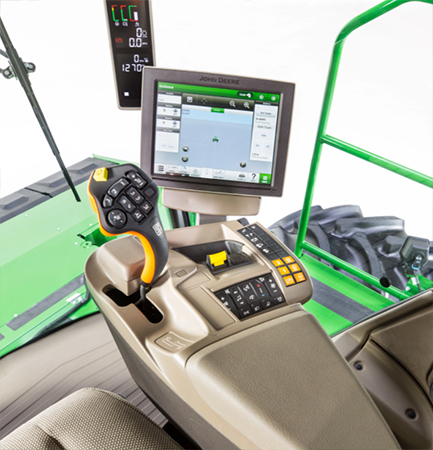
The CommandARM console provides the operator with unmatched control of the windrower and platform. Controls are designed and positioned to enhance ergonomics and are easy to locate and use. Operators will appreciate the look and feel of the control console in the windrowers, which are similar to the design used in John Deere tractors and combines.
Adjustment of the CommandARM console meets the needs of every operator. It adjusts at an angle, fore/aft, and up and down for precise operator comfort.
The CommandARM console provides access to the most frequently used windrower controls:
- Field/road speed range
- Float adjust
- Platform speed adjustments
- Throttle – low idle, variable idle, and high idle
- Platform engage/disengage
- Windrower merger speed, raise, and lower (if equipped)
- Road hazard engage/disengage
- Gen 4 CommandCenter™ display navigation
- Display menu shortcut buttons
- Climate control switches
- Worklight switches
- Beacon light switches
Multi-function lever
The controls vital to the operation of the W200 Series Windrowers are conveniently located on the multi-function lever. The ergonomic multi-function lever gives the operator fingertip control of the following functions:
- Platform float suspension adjustment
- Windrower merger position (if equipped)
- Platform presets (to raise, lower, and engage AutoTrac™ system)
- Increase/decrease cutterbar or draper speed
- Platform raise/lower
- Platform tilt
The multi-function lever is also associated with the following functions:
- Forward/reverse ground speed
- Automatically disengages the park brake when moved from the park position with the engine running
- The park brake is automatically engaged when placed in park.
- With platform enabled and on rotary traction units only, automatically raises the platform when moved from forward to reverse position
- This function prevents wrapping cut crop into condition rolls.
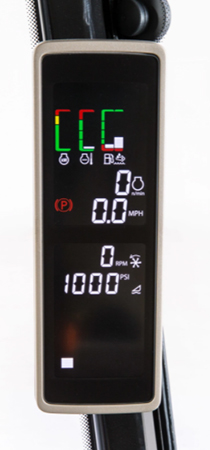
The cornerpost display features electronic instrumentation and blends well with the narrow, right-hand cab post, providing excellent visibility to the header. The cornerpost display is divided into an upper and lower region. The upper region provides traction unit information, and the lower region provides platform-specific information.
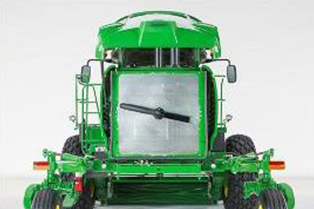
The W200 Series Self-Propelled Windrowers feature several improvements over previous designs to keep the engine operating at optimal levels and improve engine life. Design features include:
- Increased screen area of 19 percent provides more air flow through the cooling package than previous models.
- Smooth, rounded path inside the wand and ducts keeps debris from slowing and plugging.
- Air lab engineered and field-tested ducting is sized for air velocity and continual removal of debris.
- Wand backer plate helps stop debris from being sucked against the screen from the cooling fan for better cleaning performance.
- Cool air intake draws air from above the chassis, minimizing debris intake to cooling package.
- A stamped metal rear screen provides easier cleaning.
- The air conditioner condenser and oil cooler assembly swing out for easy serviceability and cleaning.
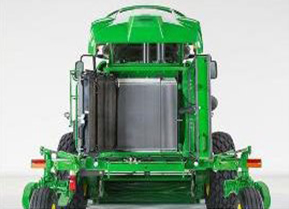
The W200 Series Windrowers are tested in tough conditions of over 37.8° C (100° F) to ensure that the drives stay properly cooled for maximum life and reliability. The 94.6-L (25-gal.) oil reservoir supplies oil to the pumps. Oil is cooled as it passes through the combination oil cooler and air conditioner condenser assembly at the rear of the machine.
Live monitoring of the hydraulic oil temperature at the left and right drive motors and reservoir limit switch protects against overheating during drive motor stall or high-grade terrain conditions
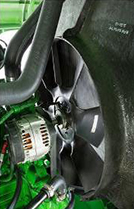
The eight-blade cooling fan incorporates a viscous drive system that provides precise control over fan speed during operation. Optimization of the viscous fan speed leads to significant reductions in parasitic losses in certain operating conditions.
The fan speed is controlled by various factors such as engine coolant temperature, intake manifold air temperature, or hydraulic oil temperature. This level of control allows the fan to operate only at the required speed to keep the engine and cooling package at optimal operating temperature and reduces engine noise levels.
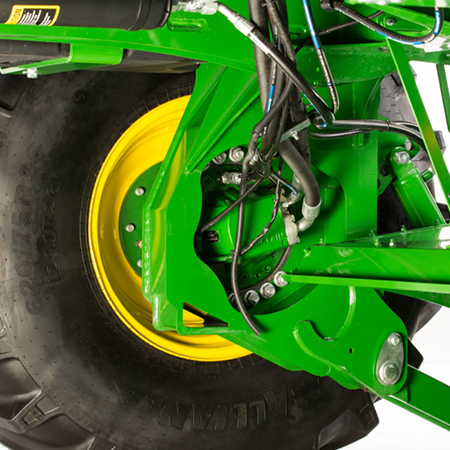
The heavy-duty drive motors provide an increased torque rating for dependable operation in borders, irrigation wheel tracks, and rough field conditions.
They come in two options for the M-spec machines: 29 or 38.6 km/h (18 or 24 mph). The R-spec machines are only available as 38.6 km/h (24 mph).
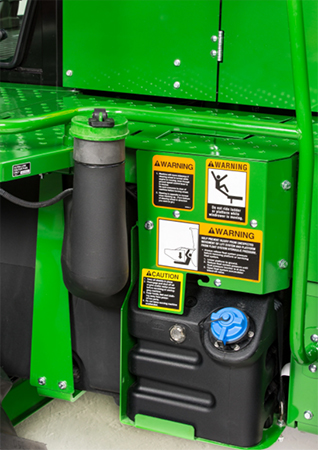
The diesel fuel and diesel exhaust fluid (DEF) fill locations on the W200 Series Self-Propelled Windrowers provide convenient filling from the ground level.
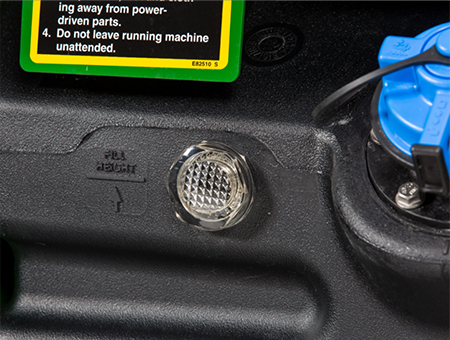
The DEF sight gauge keeps operators from overfilling the tank, preventing spills and damage from freezing and expansion in cold weather.
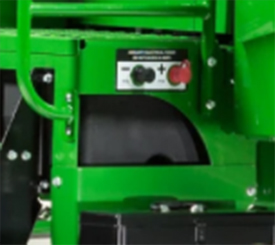
A remote batter terminal, conveniently located on the left-hand platform near the fluid fill, provides power for the 12-V fuel pumps on refueling tanks.
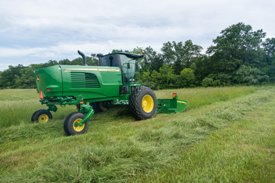
Constant header speed is a feature unique to the W200 Series Self-Propelled Windrowers. It is made possible by a state-of-the-art platform hydraulic pump control system that monitors platform speed and controls the pump to maintain a required speed. Constant header speed translates to a consistent cut quality and uniform windrow formation throughout varying crop conditions and terrain changes.
As crop conditions change, causing the header to slow, or if the engine begins to load as terrain changes, the control system diverts more oil flow to the platform drive motor to maintain the header speed set point. This widens the peak power range of the header, delivering optimal power when it is needed most.
Other advantages of constant header speed include:
- Ability to run the header at slower speeds in lighter crops, translating to less overall fuel consumption
- Ability to run engine speed under rated rpm and maintain the set header speed
- Improved ramp up and down speeds upon starting and stopping the platform, increasing life of header and platform drivetrain components
The industry-exclusive, rear-wheel steer assist system provides added control to the windrowers, enabling higher cutting and transport speeds.
IntelliAxle steer assist also has independent rear suspension, smoothing out the roughest field and road conditions and decreasing operator fatigue during long days in the field.
Independent rear suspension
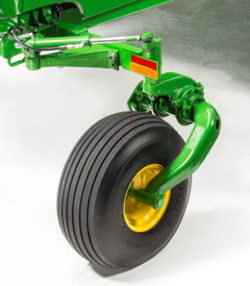
The independent rear suspension contributes to a better quality of ride and less fatigue for the operator. The torsion axle design absorbs the shock experienced in rough terrains, allowing faster cutting speeds.
Rear-wheel steer assist
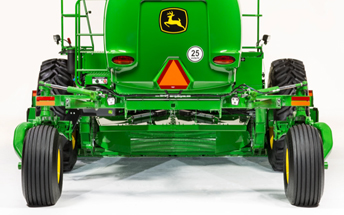
The rear-wheel steer assist system allows easier, more positive handling in the field as well as on the road during transport. Improved from the 450 Series design, the W200 Series features an electrohydraulic, proportionally controlled rear steering system that provides tighter steering and better control at higher speeds.
In-field working speeds up to 27.3 km/h (17 mph) and road speeds up to 38.6 km/h (24 mph) are achieved with the help of this improved axle design.
Smooth, fluent steering helps the operator to maintain complete control of the windrower during sharp turns and aggressive field conditions. The steering sensitivity is manually tuned by the operator using the CommandCenter™ display to match operator preference and field conditions.
The steer assist system provides three modes of steering aid as the machines travel through the speed ranges:
- Inactive
- At speeds less than 6.4 km/h (4 mph), the IntelliAxle steer assist system is not active and the front drive wheels solely control the machine steering.
- Field range
- At speeds above 6.4 km/h (4 mph), the IntelliAxle steering system begins to contribute to steering the machine by hydraulically assisting the turning of the rear caster wheels. The operator can set the desired sensitivity for the field range using the CommandCenter display.
- Transport range
- For transport range, the operator can set a different sensitivity independent from field range. If preferred, this gives the operator increased flexibility in tuning the steering system to desired sensitivity for higher transport speeds.
Faster field and transport speeds
Faster field and transport speeds are achieved with the increased controllability and stability provided by the rear-wheel steer assist system and independent rear-wheel suspension. The IntelliAxle system, when coupled with the integrated AutoTrac™ steering system, delivers unmatched performance and productivity.
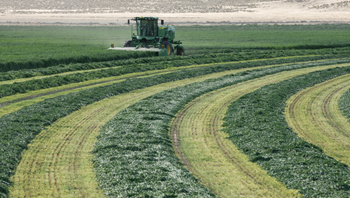
The W200 Series Self-Propelled Windrowers exhibit the industry’s first fully integrated AutoTrac steering system without the use of electrohydraulic pumps or universal type add-ons. The steering system features the industry’s only steering design, utilizing multiple steering systems to maximize controllability.
Additionally, this increased accuracy and controllability allows for faster operating speeds. Integrated AutoTrac on the W200 Series can run up to 27.4 km/h (17 mph) if conditions allow.
A unique hydraulic over mechanical design controls coarse adjustments of the drive pumps, and an electrohydraulic proportional rear steering system executes fine adjustments, delivering the most accurate steering system in its class.
W200 Series Self-Propelled Windrowers are AutoTrac ready from the factory and require only a display, AutoTrac activation, and StarFire™ receiver to enable. Click here to learn more about required components for AutoTrac on W200 Windrowers.
AutoTrac ensures more consistency and that more of the platform engages the crop at all times, leading to increased productivity. This adds value to the operation by providing more consistent windrows, longer operating hours, and less fatigue.
Integrated AutoTrac on the W200 Series far outperforms previous windrower options, delivering faster cutting speeds and more acres cut in less time.
Uneven cutting surfaces such as irrigation berms and pivot wheel tracks make for challenging cutting. The W200 Series Windrowers feature independent platform float suspension to improve cut quality on non-level surfaces and deliver improved performance.
Improved flotation on non-level surface
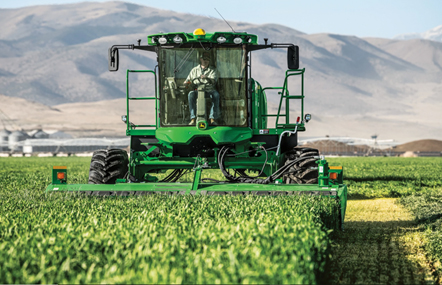
The independent float suspension delivers improved cut quality along irrigation berms and pivot tracks.
Adjusting the float suspension independently allows the platform to ride on the raised surface with proper floatation, reducing gouging and dirt buildup on the platform. Less dirt buildup means increased uptime and less dirt in the windrow, delivering higher quality hay and forage.
Adjustment to the rotary header can be made from the cab. You can adjust the formation shields and swath flap on the go.
Windrow width adjustments
To perform windrow width adjustments previously, you had to crawl under the machine to loosen and adjust the forming shields.
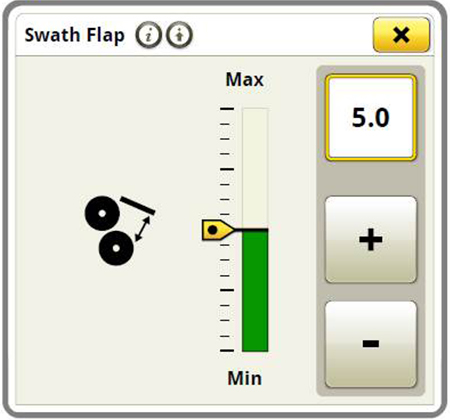
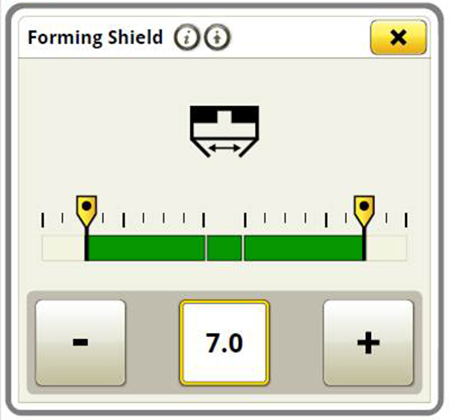
With TouchSet, the operator can select and adjust the swath flap and forming shield settings easily right from the display.
Preset adjustments
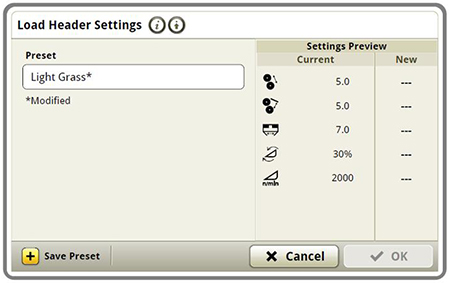
TouchSet comes with a preset library of different crops to select while cutting. The crop selection automatically adjusts the header for that particular crop.
You can also customize your own preset for a particular field and/or cutting. This allows you to quickly adjust the swath flap, forming shields, head tilt, and cutterbar speed.
Specifications
Key Specs | w200m-windrower Current Model |
---|---|
Engine - Model | 6.8L PSS Final Tier 4 |
Horsepower | At 2,400 rpm: 193.9 kW 260 hp |
Ground drive - Type | Two-speed hydrostatic |
Fuel - Capacity | 568 L 150 U.S. gal. DEF: 26.5 L 7 U.S. gal. |
Low range | 24.1 km/h 15 mph |
High range 2 speed / Mid range 3 speed | 33.8 km/h 21 mph |
Vehicle | Large drive tires and suspended rear axle in base |
Seat | Air suspension, swivel fore-aft attenuation |
Under frame clearance | 1,120 mm 44 in. |
Weight - Total | 7348 kg 16,200 lb |
Engine | |
Make | |
Model | 6.8L PSS Final Tier 4 |
Horsepower | At 2,400 rpm: 193.9 kW 260 hp |
No. of cylinders | Six |
Exhaust direction | Vertical |
Engine displacement | 414 cu in. 6.8 L |
Engine speeds | Low idle 900 rpm Variable idle Electronic adjustable from 1,700 to 2,450 rpm High idle (no load) 2,450 rpm Rated speed 2,400 rpm |
Oil crankcase capacity (with filter) | 31.4 L 33.2 U.S. qt |
Cooling system | 49.2 L 52 U.S. qt |
Bearings | |
Ground drive | |
Type | Two-speed hydrostatic |
Hydraulic platform drive | |
Number of pumps (Rotary/Auger) | One |
Number of motors (Rotary/Auger) | One |
Pump displacement | 89 cm3 5.43 cu in. |
Motor displacemen | Per revolution: 75.4 cm3 Per revolution: 4.6 cu in. |
Platform float system | |
Type | Hydraulic piston accumulator |
Final drives | |
Type | Planetary double reduction heavy duty |
Ratio | 36.8:1 |
Brakes | |
Type / Activation | Parking brake automatically engages and disengages; integrated into multifuncton control lever |
Hydraulics | |
Reservoir capacity | 94.5 L 25 U.S. gal. |
Fuel | |
Capacity | 568 L 150 U.S. gal. DEF: 26.5 L DEF: 7 U.S. gal. |
Electrical system | |
Alternator | 240 amp |
Battery | Heavy-duty 12 V |
Tires | |
Drive wheel standard | 520/80R38 radial bar |
Drive wheel option | Bias button, 480/80R38 149A8 R1 radial bar (required on 994-4m platform) |
Caster wheels | 14Lx16.1 8-ply ribbed |
Caster wheels option | |
Speeds | |
Low range | 24.1 km/h 15 mph |
High range 2 speed / Mid range 3 speed | 33.8 km/h 21 mph |
High range with 3 speed | |
Suspension | |
Vehicle | Large drive tires and suspended rear axle in base |
Cab | Large drive tires for smooth ride |
Cab | |
Construction | Uni-body, welded |
Glass | 7.08 m2 76.2 sq ft |
Seat | Air suspension, swivel fore-aft attenuation |
Steering column | Telescoping |
Instructional seat | Standard |
Windshield wiper | Single-blade or dual-blade |
Air conditioner | Refrigerant R134a Capacity 2.7 kg 6 lb Filters Dry type, reusable Compressor Rotary Overload protection Low-pressure and high-pressure cutoff Standard with automatic temperature control |
Lights | |
Front | Standard: six or eight halogen Optional: four halogen, four HID |
Side | Four optional |
Back | Two halogen standard |
HID | Optional four front |
Display and input | |
Type | Electronic touch and no touch option |
Dimensions (with platform installed) | |
Overall length without platform | 5,900 mm 225.5 in. |
Overall height | 3,760 mm 148 in. |
Under frame clearance | 1,120 mm 44 in. |
Wheelbase | 3,400 mm 142 in. |
Tread width | 3,710 mm 146 in. |
Turning radius | |
Weight | |
Without platform, full fuel | |
Front axle | 4732 kg 10,432 lb |
Rear axle | 2616 kg 5768 lb |
Total | 7348 kg 16,200 lb |
Warranty | |
Manufacturer's warranty | Full machine: 1 year Engine: 2 year; 2,000 hours |