
S770 COMBINE
Combine
- Combine Advisorâ„¢ package helps to set, optimize and automate main combine functions when conditions change
- Fully automated yield sensor calibration with ActiveYieldâ„¢ supplies accurate data with no time spent calibrating
- Comfortable S700 cab is common with tractors and sprayers for ease of use
- Continued quality manufacturing of S-Series combines maximizes uptime and productivity
View Product Brochure
Features
ActiveYield delivers automatic yield calibrations to the operator without spending time manually performing yield calibrations.
Feature benefit:
- Simplified yield calibrations for improved uptime in the field
- Simplified data collection for use during and after harvest
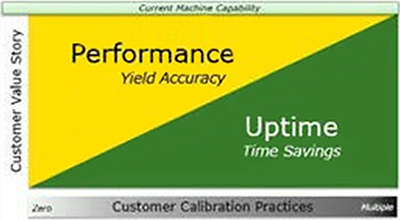
Functionality:
ActiveYield eliminates time-consuming manual yield calibrations and replaces them with automated sensors that calibrate the machine by measuring the grain as the tank fills. This enables decisions to be made in real time without leaving the cab.
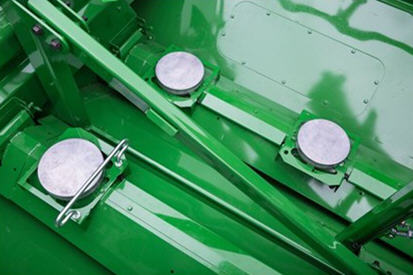
When the ActiveYield option is enabled and the Terrain Compensation Module (TCM) in the StarFire™ 3000 or StarFire 6000 Receiver has been calibrated, ActiveYield is ready to go to work. As grain is harvested and enters the tank, the three sensors within the grain tank collectively measure the grain as it piles over the cross auger covers. If all conditions are acceptable (header and separator on, grain is flowing, and machine level is within 4 degrees) load collection occurs from 900 through 3000 kg (2000 through 6600 lb).
Any pitch and roll of more than 4 degrees from center during load collection will cause the system to reject that load due to the grain pile shifting in the tank. A new calibration load starts once grain is below the sensors on the cross auger covers.
Stored calibration loads are replaced by new ones as the system continues to collect data. The system may be disabled at any time by accessing the moisture setup page and unchecking the ActiveYield box if manual yield calibration is desired.
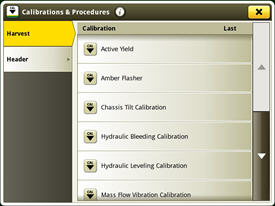
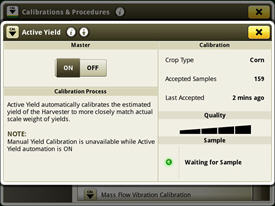
ActiveYield is available for model year 2016 through model year 2019 S760, S770, S780, and S790 Combines and requires the 4600 CommandCenter™ Display, GreenStar™ 3 2630 Display, or GreenStar 3 CommandCenter. Additionally, a StarFire 3000 or 6000 Receiver must be installed on the combine with the TCM calibrated for ActiveYield to detect machine pitch correctly. Manual yield calibration is not required as each crop has a built-in default value.
Harvest Doc™ system yield data collected by an ActiveYield system is only compatible with the John Deere Operations Center. John Deere does not guarantee compatibility of ActiveYield collected documentation with John Deere APEX™ software or third-party software systems.
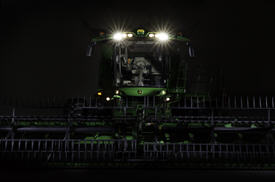
Combine Advisor is a suite of technologies designed to maximize harvesting profits. The features help the operator set and optimize the S700 Combine and then automates the combine to maintain performance target as conditions change. Purchasing Combine Advisor grants access to the Combine Advisor application, which houses three automation technologies: HarvestSmart™ system for automation of feed rate, Active Terrain Adjustment™ system for terrain change management, and Auto Maintain with ActiveVision™ cameras for crop condition change management.
Combine Advisor also provides easy navigation of the S700 set and optimize features: harvest settings application for initial set up and setting storage, VisionTrak system for monitoring losses, and Optimize Performance for step-by-step guidance of combine setting optimization. Once John Deere Combine Advisor is set into motion, the operator will experience ease-of-use benefits coupled with increased productivity.
Code | Description |
1962
| Combine Advisor Base features, plus Active Terrain Adjustment and Combine Advisor. Includes ActiveVision cameras.
Base features include Optimize Performance, TouchSet™ system, VisionTrak, HarvestSmart, and engine speed management. HarvestSmart and engine speed management only included with code 2020 (ProDrive™ transmission). Engine speed management only available with Final Tier 4 (FT4) engines. |
Combine Advisor hardware and software
Combine Advisor bundles are available for model year 2018 and future models. The bundles include ActiveVision cameras, harnesses, Auto Maintain, and software.
Dealer installation instructions are included, as weldments and drilling are required. The process will most likely take around 10 hours of labor.
Bundle | Description |
BXE11034 | Combine Advisor retrofit bundle for S760 and S770 Combines Also requires BXE10948 Active Terrain Adjustment bundle if the combine is not already equipped with code 1961 (base features + Active Terrain Adjustment) |
BXE11035 | Combine Advisor retrofit bundle for S780 and S790 Combines Also requires BXE10948 Active Terrain Adjustment bundle if the combine is not already equipped with code 1961 (base features + Active Terrain Adjustment) |
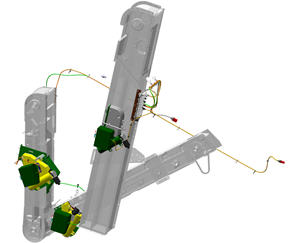
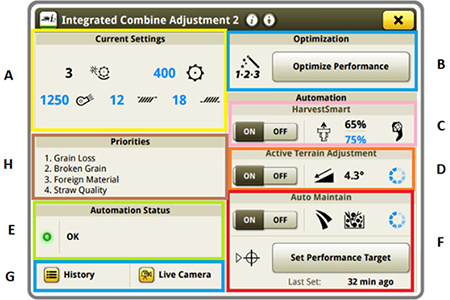
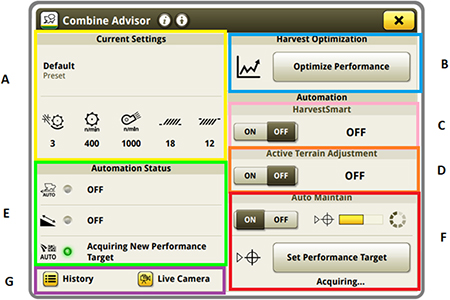
ICA2 run page, model year 2018 | Combine Advisor run page, model year 2020 |
Section A (yellow highlight): takes the operator to the current settings for concave clearance, rotor speed, fan speed, chaffer clearance, and sieve clearance, giving quick access to critical combine adjustments. | Section A (yellow highlight): takes the operator to the current settings for concave clearance, rotor speed, fan speed, chaffer clearance, and sieve clearance, giving quick access to critical combine adjustments. It also shows the currently selected preset. |
Section B (blue highlight): the Optimize Performance button helps the operator optimize combine performance. | Section B (blue highlight): the Optimize Performance button helps the operator optimize combine performance. |
Section C (pink highlight): the HarvestSmart system automates ground speed control during harvest to maintain a constant crop load. | Section C (pink highlight): the HarvestSmart system automates ground speed control during harvest to maintain a constant engine load. The Manage Target with Grain Loss setting enables an automatic target adjustment based on loss levels. |
Section D (orange highlight): the Active Terrain Adjustment system produces better grain quality and fewer losses while controlling tailings volume when harvesting up and down hills. | Section D (orange highlight): the Active Terrain Adjustment system produces better grain quality and fewer losses while controlling tailings volume when harvesting up and down hills. |
Section E (green highlight): automation status | Section E (green highlight): Combine Advisor system – HarvestSmart, Active Terrain Adjustment, and Auto Maintain. |
Section F (red highlight): Auto Maintain monitors the combine and makes adjustments to maintain the performance at the operator-set performance target. | Section F (red highlight): Auto Maintain monitors the combine and makes adjustments to maintain the performance at the operator-set performance target. |
Section G (purple highlight): Auto Maintain also uses the buttons in section G to allow a glimpse into live views of the clean grain and tailings elevators and allows operators to use an analyzer function to see what Auto Maintain is seeing. It also shows a list of adjustments made by Auto Maintain and Active Terrain Adjustment. **In sections C, D and F select the screen area to see additional sensitivity settings for each system. | Section G (purple highlight): Auto Maintain also uses the buttons in section G to allow a glimpse into live views of the clean grain and tailings elevators and allows operators to use an analyzer function to see what Auto Maintain is seeing. It also shows a list of adjustments made by Auto Maintain and Active Terrain Adjustment. **In sections C, D and E select the screen area to see additional sensitivity settings for each system. |
Section H (brown highlight): indicates the operator’s priorities for automation | --- |
![]() |
|
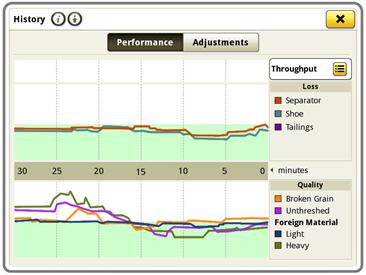
The ActiveVision cameras can detect broken and unthreshed grain. The cameras will also detect lightweight and heavy foreign material to make the appropriate combine settings changes. The system provides a live feed of both the grain and tailings cameras and will highlight the parameters outlined to make it easier to analyze. The live view and historical graphs update constantly, and the cameras will even tell the operator if there is debris on the lens.
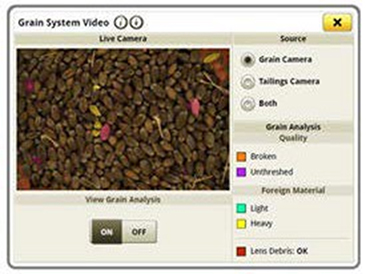
![]() | Combine Advisor with Auto Maintain is available as a factory-installed option on combines since model year 2018. Auto Maintain is compatible in corn, soybeans, wheat, canola, and barley. Retrofit kits, BXE11034 and BXE11035 are available. Please refer to that section for more information. |
Combine Advisor video
- John Deere Combine Advisor Package (full video)
- The following videos are segments of the above full version:
Combine Advisor application
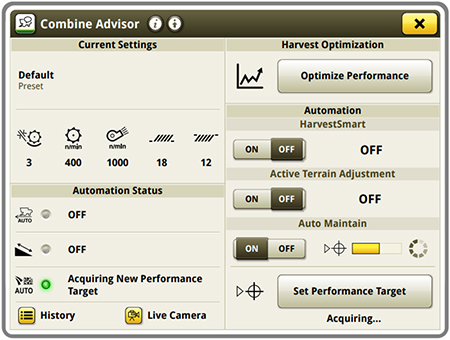
The Combine Advisor application provides the tools needed to set the combine to get the most out of it and automatically adjust settings to maintain optimum performance. Inside this application on the 4600 CommandCenter™ Display, the operator will find many tools including easy-to-adjust current machine settings, sensitivity settings for automation, application status indicators, automation activity history overviews, and live feeds of grain analysis cameras.
Additionally, the operator can access Optimize Performance, activate the three automation technologies, and set the performance targets the machine will automatically adjust to maintain.
Feature benefits:
- Efficient combine operation with a one-page application for animation technologies
- Improved combine settings management with settings, sensitivities, and status information all on one reference page
- Reduced operator training and efficient, easy control of harvest settings through an intuitive run page and user interface
Functionality:
Auto Maintain
Auto Maintain with ActiveVision cameras is technology that works to automatically adjust five primary S700 Combine settings to maintain the user set performance target. When harvesting corn, soybeans, wheat, canola, or barley, the combine will maintain the performance of everything from grain loss and grain quality, to foreign material in the grain tank. The ActiveVision cameras, along with grain loss monitors, are specifically designed to identify the impact of crop condition changes and adjust the combine to maintain the performance target, allowing the operator to focus on other challenges of harvest.
Feature benefits:
Simplify harvest by automating the critical workload of constantly managing combine settings when conditions change
Increase productivity by allowing ActiveVision cameras to identify and address tough-to-spot problems such as cracked grain
Provide flexibility in planning overall business and increase the efficiency of the combine independent of operator experience
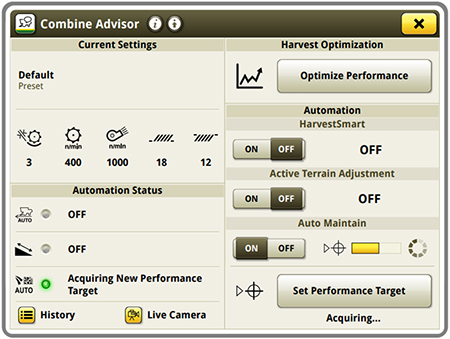
Functionality
Auto Maintain looks at the level at which the combine is performing, sets that as the goal, and automates combine settings to continually hit the target performance goal over time. Auto Maintain uses existing sensor inputs along with the ActiveVision cameras to make decisions for accurate combine adjustments. It does not use grain moisture as an input, however. Auto Maintain is able to hit the target goal by automatically making adjustments to the threshing speed, concave clearance, chaffer clearance, sieve clearance, and fan speed. The ActiveVision cameras have been trained to analyze the clean grain and tailings material and input that analysis into the Auto Maintain system. Auto Maintain will show the operator how it has been performing with a constantly updating historical graph of losses, grain quality, and foreign material in the clean grain. The green-shaded area below indicates the performance targets set. The colored lines show the ongoing levels of losses and quality. For example, the green, purple, and orange lines below show a period of time outside of the green-shaded acceptable area. Auto Maintain recognizes this and makes the appropriate adjustments to meet the set targets.
Additional Combine Advisor features
The Generation 4 CommandCenter was designed to provide a consistent user experience by providing full-screen viewing of more run page modules, shortcut keys, and precision agriculture capabilities.
Expect easier set-up, along with increased operator confidence, thanks to a simple, customizable interface. The improved design of the Generation 4 CommandCenter also aids in an optimal operating experience and maximizes uptime.
In order to increase your efficiency, take advantage of the following features offered by the Generation 4 CommandCenter:
Layout manager
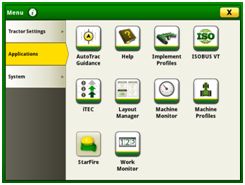
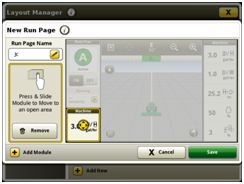
- Easily create page views that meet your needs and that are also equipped with default run pages.
- Users and access allow the owner or manager to lock out certain functions to prevent operators from accessing or changing settings with a defined four-digit code.
- Gather on-screen help by selecting the help icon on the shortcut bar on the bottom of every page.
Machine monitor
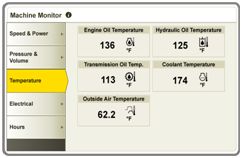
- The Machine Monitor application provides you instantaneous readings about the status or condition of your machine.
- This application shows parameters such as engine speed, coolant temperature, and ground speed.
Work monitor
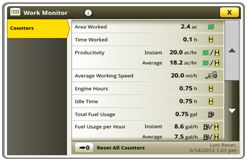
- The Work Monitor application displays performance information about the task being performed by the machine.
- You are shown averages, totals, and productivity of the machine, such as area worked, average working speed, and fuel usage.
- Work setup places the settings needed to properly setup features such as AutoTrac, Documentation, and Section Control in a single location. Settings include:
- Client, farm, and field
- Crop type
- Machine and implement dimensions
- Variety/hybrid and planting/seeding rates
- Variable rate prescriptions
- Product and application rates
- Application rates through the implement screens
Video capability
- Machines equipped with a 4200 CommandCenter are equipped with one video input, and the 4600 CommandCenter has four video inputs.
- You have the ability to set a variety of triggers. With each trigger, the image will then appear on the display.
Flags
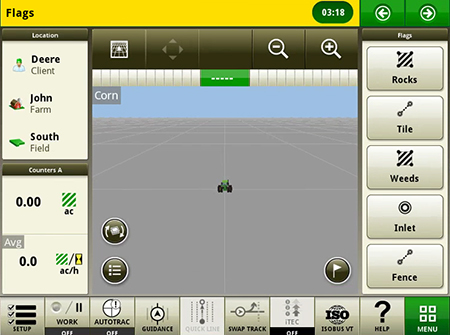
- Mark areas in the field that need special attention such as rocks, tile lines, or weed pressure.
- Flags previously recorded on the Gen 4 or GreenStar™ 3 2630 Display can be transferred between monitors.
- Flags previously recorded on the Gen 4 or GreenStar™ 3 2630 Display can be transferred between monitors.
Field boundaries
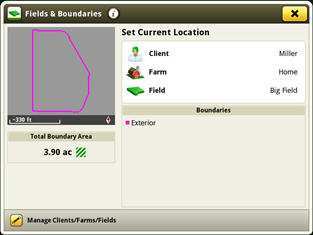
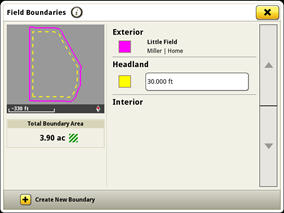
- Manually drive field boundaries with the Generation 4 CommandCenter or import existing boundary information from the GreenStar 3 2630 Display or John Deere Operations Center. Gen 4 documentation data can be used to create boundaries from coverage within the John Deere Operations Center.
Dual-display mode
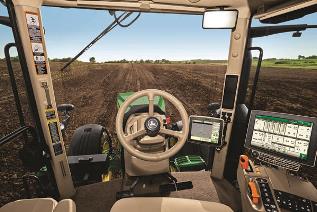
- Generation 4 CommandCenter may be configured to run with the following John Deere displays connected at the cornerpost of a John Deere tractor:
- GreenStar 2 1800 Display
- GreenStar 2 2600 Display
- GreenStar 3 2630 Display
- 4640 Universal Display
- 4240 Universal Display
NOTE: Vehicle applications will always be located on the Gen 4 CommandCenter.
Automatic base station switching
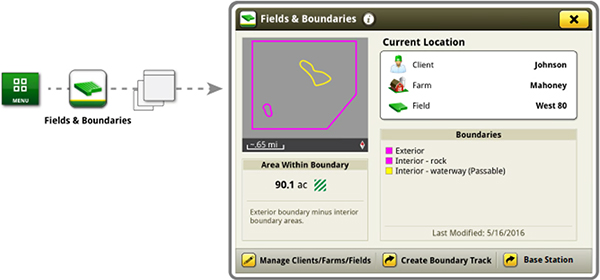
- Customers using John Deere RTK Radio 450 or 900 can link a base station to a desired client,/ farm,/ or field. This allows automatic switching to the associated base station when changing fields. The ability to import base station assignments into Operations Center and send back to machines will be available at a later date.
Video looping supported with Gen 4 4600 CommandCenter Display and 4640 Universal Display
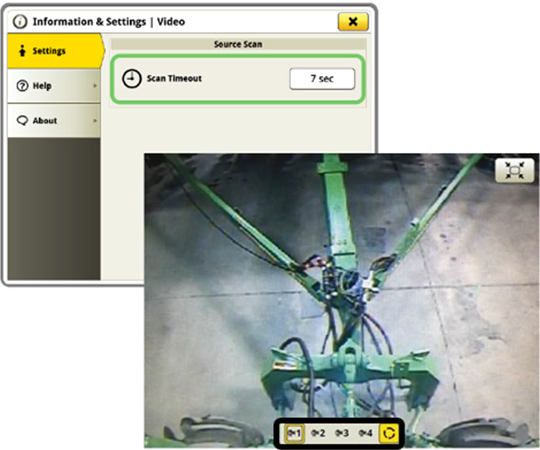
- This feature enables users to scan or loop through all of the available video feeds for a specified duration. The default scan time is set to 7 seconds per image. The scan time is customizable per image allowing for consistent visibility to all video feeds.
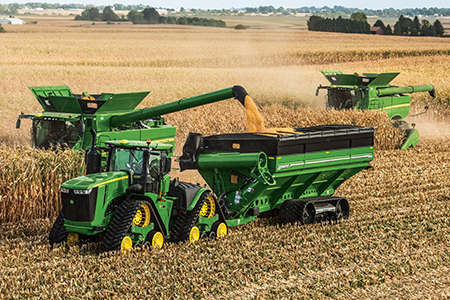
Harvest is hectic. Producers are focusing on getting all the crop from the field to the bin within a tight harvest window. Using Machine Sync, those producers can focus more on grain harvest and grain quality, and worry less about keeping the grain cart under the spout when unloading on the go. Gen 4 Machine Sync provides a solution to harvest stress by creating a wireless network between the tractor and combine to enable on-the-go unloading by synchronizing tractor speed and direction of travel with the combine.
Machine Sync works with In-Field Data Sharing to show the location of all combines and tractors within the fleet of Gen 4 machines harvesting in the field. Knowing the exact location of multiple combines as well as their grain tank fill level and unloading auger status allows the grain cart operators to be in the right place at the right time.
The Dyna-Flo Plus cleaning shoe is the heart of the S700 Combine cleaning system. The system is made up of a unique design consisting of aluminum and high-strength steel that reduces overall weight while maintaining overall strength. The Dyna-Flo Plus cleaning shoe also features an enhanced drive system that requires only one flywheel for optimal shoe performance and maximizes uptime.
Feature benefit:
- Increased size of the sieve area by 12 percent for up to an additional 0.6 ha (1.5 acres) per hour of productivity.
- Tailings volume reduction of up to 28 percent in coarse grains and up to 14 percent in small grains.
- Weight reduction of 180 kg (396 lb) for smoother operation and reduced combine ground compaction.
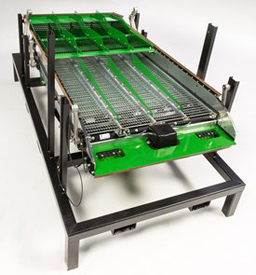
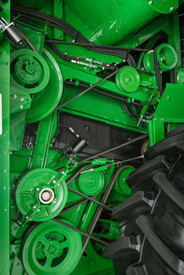
Functionality:
The Dyna-Flo Plus cleaning system begins with conveyor augers located beneath the concave area, where the volume of threshed material is highest, to evenly move material onto the cleaning shoe (1). The deep auger troughs provide uniform distribution of material to the cleaning shoe with less bunching, even on sloping terrain and when harvesting up and down hills.
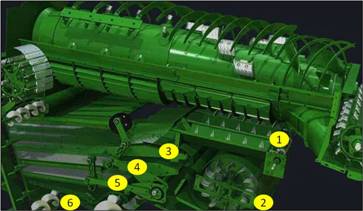
Once grain is on the cleaning shoe, the raised-center front chaffer cleans up to 40 percent of free grain before it reaches the main chaffer (3). High-velocity air from the cleaning fan elevates any light material traveling over the end of the front chaffer, resulting in more aggressive separation of chaff and increased cleaning performance (2). The main chaffer provides grain separation from chaff as the grain passes through the main chaffer to the sieve (4).
The sieve provides proper sizing of grain from material other than grain (5). Any grain that passes through the sieve is elevated to the grain tank while some grain or material other than grain flows to the tailings return system for reprocessing. On S760, and S770 Combines, the tailings material is directed back into the threshing section of the separator for additional threshing. The tailings material on the S780 and S790 Combines are directed to the active tailings return system for additional threshing, and then directed back on the return pan and then onto the main chaffer for additional cleaning (6).
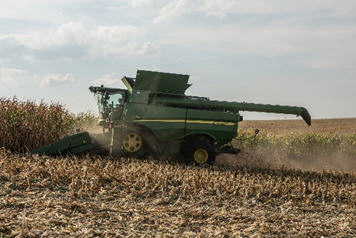
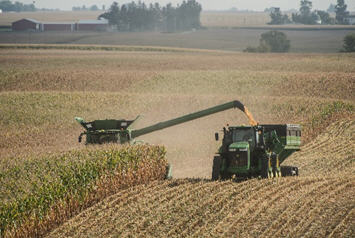
The industry-exclusive ProDrive system uses PowerShift™ transmission technology to automatically shift between two speed ranges as ground conditions and terrain change to keep the combine harvesting at the desired ground speed. Valuable harvest time will no longer be lost shifting on hills and when exiting fields to start transporting.
Feature benefit:
- Precise control of the combine speed (when going up or down hills) without the need to continuously monitor and adjust the multifunction control lever
- Retain high levels of productivity through the speed ranges with shift-on-the-go technology
- Maintain ground speed when engaging four-wheel drive (4WD) (if equipped)
- Operator-selected maximum speed within each range, allowing for more precise control of the combine in delicate operations (for example, when hooking up headers)
The ProDrive system on S700 Combines includes an integrated HarvestSmart™ feedrate control system to provide the maximum productivity and reduce operator stress and fatigue.
Functionality:
The ProDrive hydrostatic motor has a higher displacement than the previous hydrostatic systems. Both the pump and motor are variable-displacement components that allow ProDrive to maintain high levels of torque to the ground throughout each of the two operating-speed ranges.
Range one can be set for typical harvesting speeds. Range two can be used when higher speeds are needed during harvest or when transporting the combine.
The ground speed can be infinitely varied within both modes by the operator, using the multifunction control lever on the CommandARM™ armrest console. The multifunction lever regulates the high-capacity, variable hydrostatic pump and motor that drives the ground speed.
Using the navigation tools on the armrest, the operator can dial in the desired maximum-attainable speed within each of the two speed ranges. The maximum forward speed in either range can be set from 0 to 38.6 km/h (0 to 24 mph). The maximum speed in range one cannot be set higher than the maximum speed for range two. For example, if a maximum harvest speed of 13 km/h (8 mph) is desired and set, the full forward position of the hydrostatic control handle will deliver the speed of 13 km/h (8 mph).
The ProDrive transmission is equipped with an electrohydraulic differential lock with a four-pinion differential. Non-ProDrive combines have a two-pinion differential. When operating in muddy, hilly terrain or in sandy conditions that may cause one of the tires to lose traction, this differential lock enables the operator to maintain productivity. If traction is lost, the operator can quickly and easily engage the differential lock by pressing the differential lock button on the CommandARM armrest console. An indicator light within the button alerts the operator that the differential locking feature is engaged.
Platform tilt allows operators to hydraulically adjust the fore-aft pitch of front-end equipment at the touch of a button from inside the cab to adapt to changing crop and field conditions.
Feature benefit:
- Maximizes performance of header in down crop or changing field conditions to extend the harvest day by up to one hour
- Achieves customized fore-aft angle of header with 17 degrees of tilt
- Adjusts from inside the cab, on the go
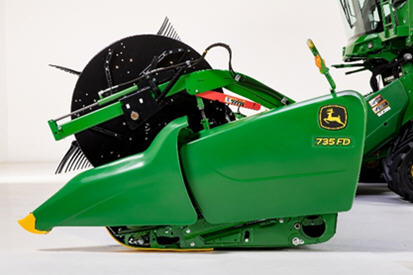
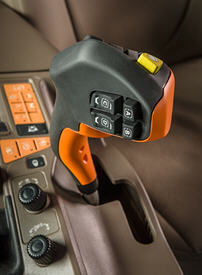
The platform tilt feature includes a different multifunction lever (hydro handle) to adjust the feederhouse tilt frame from the cab.
Functionality:
All S700 Combines provide an optional hydraulic header fore-aft tilt capability from the cab. However, all S700 Combines include a front-tilting faceplate as standard equipment. This tilting faceplate allows static fore-aft adjustment of up to 17 degrees of tilt on the feederhouse to accommodate different header and tire combinations to ensure a parallel cutterbar-to-ground relationship. This prevents the cutterbar knife guards from bulldozing or the platform healing on the rear of the skid shoes.
NOTE: Hydraulic fore-aft adjustment range is limited based upon the front-end equipment attached to prevent header frame damage. Check availability in local Price Pages.
The TriStream rotor is unique to John Deere because it features a slightly tapered design in the threshing area for best-in-class grain quality while dramatically reducing the growling that often comes with heavy rotor loads. The TriStream rotor is recommended for producers who harvest mainly coarse grains along with easy-threshing small grains.
The spiral vanes surrounding the rotor guide the crop material through the threshing and separating area in a pull-and-release action to improve performance. This John Deere S700 Combine feature will generate less power consumption.
Feature benefits:
- TriStream rotor technology reduces the force required to move material through the combine by as much as 20 percent, maximizing fuel efficiency.
- The rifling grooves on the threshing elements allow the bullet-shaped rotor to move material more efficiently, maximizing crop threshing performance and grain quality.
- Heavy-duty vanes on the top covers propel the crop smoothly rearward through the length of the rotor, ensuring all the threshed grain is separated.
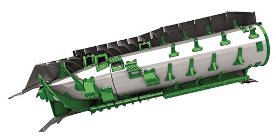
Functionality:
Fifteen cast-constructed threshing elements provide superior material handling with excellent grain quality. The elements spiral around the rotor to control material flow. In some harvesting environments, the dense-pack configuration (nine additional threshing elements) may be necessary.
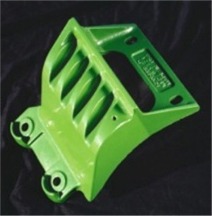
Conical top covers allow for smooth material movement within the threshing and separating area. The top covers have a radius larger than the rotor, allowing the material to expand as it travels along the top of the rotor. This design uses the pull-and-release action of crop material, aiding in the threshing and separating to reduce power consumption.
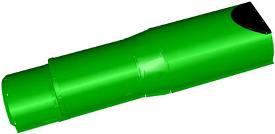
The industry-exclusive variable-stream rotor features a tapered design in the threshing section, which improves crop flow, enhances grain quality, and reduces power consumption. The variable-stream rotor with adjustable top cover transport vanes is recommended for producers of rice and in tough threshing conditions.
The variable-stream rotor smooths crop flow during tough handling conditions to maximize throughput. Along with the tough-material handling capabilities of the variable-stream rotor configuration, the straw quality and length can be improved due to the electrically adjustable top cover transport vanes.
Feature benefits:
- The longer rotor taper in the threshing area allows improved material handling by providing smoother crop flow through the combine, maximizing threshing performance and fuel efficiency.
- Electrically adjustable transport vanes allow operators to change the vane angle from the cab for improved straw quality.
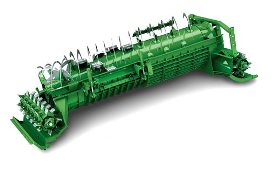
Functionality:
Fifteen cast-constructed threshing elements provide superior handling, improved durability and serviceability, and maintain excellent grain quality. The elements spiral around the rotor to move and control the material. In some harvesting conditions, 12 additional bolt-on threshing tines may be installed for increased material handling.
Rear discharge flights and a tapered rear cone improve material handoff to the rear discharge beater.
Electrically adjustable transport vanes allow operators to change the vane angle within the cab. Longer straw length can be accomplished when vanes are in the advanced position.
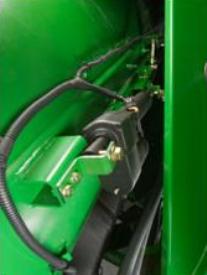
Specifications
Compare the specifications of up to 4 models
Key Specs | s770-combine Current Model |
---|---|
Engine type | John Deere PowerTechâ„¢ PSS engine 9 L 548 cu in. |
Rated power | 292 kW 391 hp |
Fuel capacity | 950 L 250 gal. |
Rotor length | 312 cm 123 in. |
Rotor diameter | 76.2 cm 30 in. |
Concave area | 1.1 m2 11.8 sq ft |
Separating area | 1.54 m2 16.6 sq ft |
Total cleaning area (louvered) | 5.1 m2 54.9 sq ft |
Grain tank size | 10,600 L 300 bu |
Unloading rate | 116.3 L/s 3.3 bu/sec |
Engine | |
Engine type | John Deere PowerTech PSS engine 9 L 548 cu in. |
Emission level | Final Tier 4 / Tier 2 (Australia/New Zealand) |
Rated speed | 2,200 rpm |
Rated power | 292 kW 391 hp |
Power boost @ rated speed | 25 kW 34 hp |
Fuel capacity | 950 L 250 gal. |
Engine family | |
Feeding | |
Drive type | Fixed or variable or multi-speed |
Conveyor chain slat type | Cast iron |
Width | 139.7 cm 55 in. |
Length | 172.5 cm 67.9 in. |
Feed Accelerator, Stone Trap (FAST) | Reverser Standard Standard |
Threshing/ Separating | |
Separator type | Rotary |
Rotor length | 312 cm 123 in. |
Rotor diameter | 76.2 cm 30 in. |
Rotor speed range | 210-1,000 rpm |
Concave area | 1.1 m2 11.8 sq ft |
Separating area | 1.54 m2 16.6 sq ft |
Discharge grate area | 0.36 m2 3.9 sq ft |
Cleaning | |
Front chaffer | 0.5 m2 5.4 sq ft |
Front chaffer extension | |
Pre cleaning | |
Chaffer | 2.5 m2 26.9 sq ft |
Sieve area | 2.1 m2 22.6 sq ft |
Total cleaning area (louvered) | 5.1 m2 54.9 sq ft |
Cleaning fan speed | 620-1,350 rpm |
Grain handling | |
Grain tank size | 10,600 L 300 bu |
Unloading auger length | 6.9, 7.9 or 8.7 m 22.5, 26 or 28.5 ft |
Unloading rate | 116.3 L/s 3.3 bu/sec |
Base weight - less head | |
Manufacturing location | |